Материалы для ювелирных изделий
Шрифт:
Объемная усадка металла – изменение объема металла при его охлаждении, которое практически зависит от изменения температуры (если нет агрегатных или аллотропических превращений):
V 1 = V 0 [1 – αν ( t 0 – t 1)],
где V 1 – объем при данной температуре t 1; V 0 – начальный объем при температуре t 0; αν – коэффициент объемной усадки (сжатия), т. е. коэффициент, соответствующий усадке при понижении температуры на 1° в интервале t 0 – t 1.
Объемная усадка определяется различием плотности сплава в жидком и твердом состояниях, величиной интервала кристаллизации и характером кристаллизации внутри интервала.
Полная объемная усадка металлов и сплавов происходит в несколько этапов: усадка в жидком состоянии при охлаждении, усадка при затвердевании и усадка в твердом состоянии – и, соответственно, является их суммой. Это одно из основных литейных свойств, определяющих качество отливки.
Усадка металла в жидком состоянии — изменение объема жидкого металла при его охлаждении до температуры ликвидуса ( t л), в результате чего уровень жидкого металла понижается, а сечение остается неизменным и рассматривается как объемная усадка. Для сплава данного состава усадка в жидком состоянии (ε V ж) является переменной величиной, зависящей от коэффициента объемной усадки жидкого металла (α V ж) и от температуры заливки ( t ж):
ε V ж = α V ж ( t ж – t л).Усадка металла при затвердевании — это изменение объема металла при переходе из жидкого состояния в твердое, реализующееся в основном в интервале температур между линиями ликвидуса и солидуса. Объем может уменьшаться (например, при затвердевании стали) или увеличиваться – предусадочное расширение (например, при затвердевании чугуна).
Чем шире температурный интервал затвердевания сплава и меньше скорость охлаждения, тем шире область одновременной кристаллизации и усадки, когда идет усадка каркаса, уже закристаллизовавшихся дендритов, вокруг которого остается еще не закристаллизовавшийся жидкий расплав. Объемные изменения (понижение уровня жидкого металла относительно затвердевающей наружной оболочки отливки), связанные с охлаждением сплава от температуры заливки до температуры полной кристаллизации, приводят
Существует зависимость усадки и склонности к растрескиванию при кристаллизации от положения сплавов на диаграмме состояния (рис. 5.6).
Усадка металла в твердом состоянии – изменение объема и линейных размеров закристаллизовавшейся отливки во время ее остывания.
Рис. 5.6. Схема влияния состава сплава на усадку: для сплавов типа твердых растворов (слева) и для сплавов с ограниченной растворимостью и эвтектикой (справа).
(1 – линия начала линейной усадки.)Различают свободную усадку металла, т. е. уменьшение линейных размеров охлаждающейся в твердом состоянии отливки при отсутствии торможения усадки (механического и термического) и затрудненную усадку при наличии торможения. Под механическим торможением усадки понимают сопротивление, создаваемое литейной формой при усадке выступающих частей отливки или стержнями при усадке ее внутренних полостей. Термическое торможение усадки определяется также конфигурацией отливки и формы. В данном случае различают свободные конструкции отливок, в которых усадка каждого элемента отливок происходит независимо, и связанные конструкции, в которых усадка элементов отливок не может протекать свободно и независимо.
Линейная усадка металлов и сплавов отражает изменение линейных размеров отливки после образования на ее поверхности жесткого кристаллического скелета и охлаждения отливки до комнатной температуры.
Для металлов и сплавов, которые кристаллизуются при постоянной температуре, линейная усадка проявляется только после затвердевания расплава, т. е. температура начала линейной усадки соответствует температуре плавления. Для сплавов, кристаллизующихся в интервале температур, линейная усадка может проходить при наличии остаточной жидкой фазы.
Мерой линейной усадки металлов и сплавов служат коэффициент термического расширения и температура плавления.
Линейная усадка пропорциональна линейному коэффициенту термического расширения и разности между температурами плавления и комнатной:
ε = α t ( t пл – t 20) × 100,
где ε – коэффициент линейной усадки в процентах α t – средний линейный коэффициент расширения металла в интервале от t пл до t 20; t пл и t 20 – соответственно температуры плавления и комнатная. На величину усадки также влияют фазовые превращения, происходящие в твердом металле при охлаждении. При легировании и понижении линии солидуса линейная усадка сплавов чаще всего уменьшается.
Склонность к образованию трещин
Виды трещин
При охлаждении металлов и сплавов возникают термические и механические воздействия. Это приводит к возникновению напряжений, которые нарушают сплошность отливок, что проявляется в виде щелевидных разрывов (трещин). По времени появления трещины можно разделить на горячие и холодные. Холодные трещины возникают в материале при низких температурах, их поверхность блестящия. Горячие трещины возникают при высоких температурах (в интервале температур затвердевания). Располагаются они по границам кристаллов, имеют неровную окисленную поверхность (так как при температурах их образования активно идут окислительные процессы), на которой иногда видны дендриты.
Трещиноустойчивость – способность сплава противостоять образованию трещин в литых образцах. Изменение трещиноустойчивости сплавов связано с характером кристаллизации, проявлением линейной усадки, прочностью и пластичностью сплава в эффективном интервале кристаллизации. Разрушение затвердевающего образца происходит в тех случаях, когда начавшаяся линейная усадка вызывает такую пластическую деформацию, которая превосходит пластичность сплава при данных условиях.
Горячеломкость. Возникновение горячих трещин в отливках при охлаждении может быть объяснено существованием двух фаз (кристаллической и жидкой, в виде прослойки между кристаллами твердой фазы) в эффективном интервале кристаллизации, т. е. между линией начала усадки и линией солидуса.
Таким образом, горячеломкость – это склонность металлов и сплавов к хрупкому межкристаллитному разрушению при наличии жидкой фазы по границам зерен.
На рис. 5.7 представлен график изменения трещиноустойчивости (и горячеломкости) в зависимости от состава сплава на диаграмме состояния.
Возникновение трещин в отливках из сплава, подверженного этому явлению (т. е. с широким интервалом кристаллизации), зависит от равномерности сечения отливки и технологических режимов литья.
Заливка в холодную форму сплавов с широким интервалом кристаллизации способствует появлению большого температурного градиента между лицевой поверхностью отливки и ее центром. В таких условиях и при затрудненной усадке чаще всего возникают горячие трещины в отливках.
Отсутствие горячих трещин в отливках из чистых металлов, эвтектик и сплавов с узким интервалом кристаллизации может быть объяснено тем, что затвердевание проходит одновременно по всему объему, без образования закристаллизовавшегося остова, прослойка жидкости отсутствует, дендриты не отделяются один от другого и не нарушается сплошность наружной поверхности отливок.
Взаимодействие металлов с газами (взаимная инертность, нерастворимость, образование растворов)
Качество отливки во многом зависит от взаимодействия металлов (особенно жидких расплавов) с газами.
При изготовлении литых деталей насыщение металла газами может происходить в процессе плавки при применении влажных шихтовых материалов, за счет атмосферы плавильной печи, вследствие протекания реакций между металлом и шлаком, а также за счет газов, выделяющихся во время заливки из материалов литейной формы. Отмечается усиленное поглощение газов при нагреве до температуры плавления и увеличение газонасыщения расплава вплоть до начала кипения металла. Выделяющиеся при кипении расплава пары предохраняют его от насыщения газами, и растворимость газов в металле резко снижается.
В сплавах, содержащих компоненты, температура кипения которых сравнительно невысокая, поглощение газов незначительно.
Основная масса газов выделяется в период затвердевания сплава, что приводит к образованию газовых раковин вследствие затвердевания в первую очередь поверхности отливки и из-за того, что газы не успевают выделиться и остаются в металле под затвердевшей коркой.
Газы в металлах и сплавах находятся в виде жидких и твердых растворов, в виде химических соединений и в свободном виде.
Возможны три случая взаимодействия газов с расплавами.
1. Полная взаимная инертность. Она наблюдается, например, при плавлении любых металлов в среде инертных газов (аргона, гелия и др.).
2. Газ практически нерастворим в металле. Образующиеся химические соединения в виде жидких капель, плен или кристаллов, проникая в металл, загрязняют его.
3. Газы образуют с металлом растворы. Количество растворенного в металле газа т зависит от давления газа Р и температуры Т:
где k— постоянный коэффициент, R— газовая постоянная, Δ Q— теплота растворения 1 моля газа в расплаве. Значение Δ Q может быть положительным и отрицательным.
При Δ Q > 0 процесс растворения газа сопряжен с поглощением теплоты и является эндотермическим. В этом случае повышение температуры вызывает увеличение содержания газа в металле (рис. 5.8, кривая 1). При Δ Q < О растворение газа сопровождается выделением теплоты, т. е. является экзотермическим процессом, и повышение температуры вызывает снижение содержания газа в растворе (рис. 5.8, кривая 2). Температура плавления при Δ Q > 0 (t\'nл) меньше, чем при Δ Q < О (t"nл).
Рис. 5.8. Зависимость растворимости газов в металлах от температуры:
1 – эндотермический процесс; 2 – экзотермический процессПри эндотермическом процессе вследствие избыточного для низких температур количества газа в расплаве в ходе кристаллизации образуются пузыри, которые и являются причиной возникновения газовой пористости.
В литейных сплавах могут находиться следующие газы: H2; N2; O2; CO; Co2; CH4.
В таблице 5.1 приведены данные о взаимодействии жидких металлов с различными газами. Знак «+» указывает на значительную растворимость, знак «→ на незначительную растворимость.Таблица 5.1
Взаимодействие жидких металлов с газами
Взаимодействие с водородом. Водород составляет 80–90 % всего объема растворенного газа. Попадание водорода в жидкие металлы вследствие разложения воды или углеродов и его растворение, сопровождающееся поглощением теплоты (характерное для металлов ряда Mg – Fe), приводит к образованию газовых раковин и трещин. Растворение водорода в титане является экзотермическим процессом, растворимость растет с понижением температуры, что делает образование водородной пористости невозможным.
Взаимодействие с кислородом. Все жидкие металлы взаимодействуют с кислородом.
Легкоплавкие металлы от олова до алюминия (таблица 3.1) – практически не растворяют кислород. Взаимодействие этих металлов с кислородом сводится к образованию оксидных плен на поверхности металла.
Остальные металлы способны растворять кислород, но до определенного количества, после чего начинается образование оксидов.
Взаимодействие с водой. Большая часть металлов в жидком состоянии разлагает воду. Результаты взаимодействия расплава с водой зависят от характера его взаимодействия с водородом и кислородом.
Если расплав растворяет и кислород, и водород, то образуются растворы кислорода и водорода в металле и, как следствие, газовая пористость, вызванная выделением кислорода и водорода из расплава при затвердевании.
Если расплав не растворяет ни водород, ни кислород, то в результате контакта с влагой расплав покроется пленкой
оксидов, а водород уйдет в атмосферу. Так ведут себя олово, цинк, свинец и все сплавы на их основе. Если расплав не растворяет кислород, но растворяет водород, то происходит окисление поверхности расплава и насыщение его растворенным водородом.
Взаимодействие с азотом. Растворение азота в марганце, никеле и железе является эндотермическим процессом, вследствие чего данные металлы подвержены образованию газовой пористости, вызванной выделением азота из расплава. В титане растворение азота является экзотермическим процессом, что исключает образование газовой пористости.
Растворение азота в расплавах металлов и их сплавов в общем случае пропорционально содержанию компонентов. Исключение составляют сплавы железа и никеля с добавками алюминия и титана вследствие образования нитридов титана и алюминия в виде включений.
Для металлов ряда от олова до меди азот является практически инертным газом (таблица 5.1).
Взаимодействие с оксидом углерода. Свинец, олово и медь с оксидом углерода не взаимодействуют, для этих металлов он является практически нейтральным. Для цинка, магния, алюминия СО является окислительным газом, взаимодействие с ним приводит к образованию нерастворимых оксидов на поверхности расплава. В случае остальных металлов, приведенных в таблице 9, при охлаждении кислород и углерод взаимодействуют с образованием оксида углерода СО, и их расплавы при охлаждении и кристаллизации могут поражаться газовой пористостью, образованной оксидом углерода.
Склонность к газонасыщенности
В расплавленном сплаве всегда находятся в растворенном состоянии газы – водород, азот, кислород и др. При затвердевании и последующем охлаждении растворимость газов уменьшается, и в результате их выделения в теле отливки могут образовываться газовые раковины и поры.
Под газопасыщеппостью ( газосодержанием) понимают содержание в металлах и сплавах элементов или химических соединений, которые в свободном состоянии и нормальных условиях являются газообразными. Г азонасыщенность зависит от интенсивности двух взаимнопротивоположных процессов: поглощения газов при расплавлении металла и выделения их
Растворимость газов зависит от химического состава сплава, его температуры и других факторов. Для уменьшения газонасыщенности сплавов применяют плавку в вакууме или в среде инертных газов, а также дегазацию вакуумированием в специальных камерах и т. д.
Склонность к ликвации (дендритной, зональной, по плотности)
Ликвация – это неоднородность сплава по химическому составу, структуре, образующаяся при его кристаллизации.
Ликвация обусловлена тем, что сплавы, в отличие от чистых металлов, кристаллизуются в интервале температур. Кристаллы, последовательно выпадающие в интервале температур затвердевания, отличаются друг от друга по химическому составу. Чем раньше выпал кристалл, тем меньшее количество более легкоплавких компонентов он содержит. Естественно, что остающаяся часть жидкого сплава все время обогащается ими и остаток жидкости, застывающий последним, содержит наибольшее количество легкоплавких компонентов. Чем шире температурный интервал кристаллизации сплава, тем сильнее развивается ликвация. Ликвация является нежелательной, так как ухудшает многие свойства (механические, коррозионную стойкость и др.) сплава как в состоянии полуфабриката, так и в готовом изделии.
Различают внутрикристаллическую, или дендритную, ликвацию, которая проявляется в объеме отдельных зерен (кристаллитов, дендритов), зональную ликвацию, наблюдаемую во всем объеме отливки и ликвацию по удельному весу.
Внутрикристаллическая (дендритная) ликвация . Этот вид ликвации обнаруживается в зернах кристаллических фаз переменного состава, т. е. в зернах твердых растворов, за счет того, что кристаллизация сплава происходит в интервале температур, и при этом химический состав обеих фаз переменен.
Механизм кристаллизации при этом диффузионный, избирательный. Изменение составов жидкой и твердой фаз осуществляется за счет диффузионных процессов. При очень медленном охлаждении дендритная ликвация не наблюдается, что объясняется достаточно полным протеканием диффузионных процессов. В реальных условиях наиболее часто происходит ускоренное охлаждение отливок. Тогда диффузионные процессы в твердом растворе не успевают выравнивать состав растущих зерен по объему, и их химический состав оказывается неоднородным по сечению.
Сплав с внутрикристаллической ликвацией имеет пониженную пластичность и низкую стойкость против коррозии.
Внутрикристаллическая ликвация будет проявляться тем сильнее, чем больше различаются химические составы жидкой и твердой фаз, т. е. чем больше расстояние до горизонтали между линиями ликвидуса и солидуса на диаграмме состояния системы. Степень развития внутрикристаллической ликвации также сильно зависит от скорости охлаждения. Увеличение скорости охлаждения повышает переохлаждение сплава в процессе его кристаллизации и замедляет диффузионные процессы. Следовательно, чем быстрее охлаждается сплав, тем более развита в нем дендритная ликвация. Однако замечено, что в некоторых сплавах при очень высоких скоростях охлаждения дендритная ликвация ослабляется, диффузионный (избирательный) механизм кристаллизации постепенно заменяется бездиффузионным, когда растущие кристаллы присоединяют к себе все атомы компонентов из жидкой фазы, окружающей кристалл. Тогда химический состав кристаллов по всему своему объему оказывается равным химическому жидкой фазы, и следовательно, ликвация отсутствует.
Для уменьшения внутрикристаллической ликвации сплавы в виде слитков или отливок подвергают диффузионному отжигу (гомогенизации). Металл нагревают до возможно высокой температуры, чтобы только не допустить оплавления, и выдерживают длительное время. При этом в неоднородных по химическому составу зернах твердого раствора дополнительно развиваются процессы диффузии, в результате чего выравнивается их химический состав.
Зональная ликвация. Зональная ликвация встречается в различных формах.
Ликвация по поперечному сечению слитка. Чаще всего такая проявляется в том, что наружные слои слитка по сравнению с центральной зоной обогащены компонентом, повышающим температуру кристаллизации сплава. Такая зональная ликвация называется прямой. Объясняется она естественным ходом кристаллизации слитка в изложнице, когда сначала формируются его наружные слои, а потом внутренние. Но при этой последовательности во внутренних частях слитка кристаллизующаяся жидкая фаза согласно ходу линии ликвидуса на диаграмме состояния обогащается компонентом, снижающим температуру кристаллизации сплава. Поэтому в застывающем слитке при движении от его поверхности к центру уменьшается концентрация компонента, повышающего температуру кристаллизации, и соответственно растет концентрация компонента, снижающего температуру кристаллизации. Установлено, что в крупных слитках, охлаждающихся медленно, прямая зональная ликвация развита сильнее, чем в слитках малого сечения, которые охлаждаются быстрее.
Значительно реже встречается так называемая обратная ликвация, когда наружные слои слитка обогащены компонентом, понижающим температуру кристаллизации сплава. В заключительной стадии кристаллизации слитка жидкая фаза, обогащенная легкоплавким компонентом и находящаяся во внутренних объемах слитка, под влиянием давления от выделяющихся из расплава газов по междендритным каналам и другими путями продавливается к наружным слоям слитка и тем самым искусственно повышает в них концентрацию этого легкоплавкого компонента.
Прямая и обратная зональные ликвации не уничтожаются ни диффузионным отжигом, ни горячей пластической деформацией. Для уменьшения развития зональной ликвации по поперечному сечению слитка применяют специальные меры по созданию нужной формы слитка и условий их охлаждения.
Ликвация по удельному весу (по высоте отливки). Этот вид ликвации проявляется в том, что средний химический состав верха отливки отличается от состава низа отливки. Это обусловлено различием в структуре его верхних и нижних частей за счет того, что сплавы кристаллизуются как смесь различных фаз при условии заметной разницы в величине удельного веса у компонентов, например сплавы системы сурьма – свинец. В этих сплавах при медленном их охлаждении при кристаллизации создаются условия, когда тяжелые кристаллические образования опускаются к низу отливки, а более легкие – всплывают к верху отливки. Особенно резко проявляется ликвация в цветных сплавах. Например, в свинцовистых бронзах наиболее заметна ликвация свинца потому, что его удельный вес равен 11,3 г/см3, что намного больше среднего удельного веса сплава (порядка 8,6 г/см3).
Ликвация по удельному весу развита тем сильнее, чем медленнее охлаждается сплав. Следовательно, для предотвращения образования ликвации по удельному весу сплавы следует охлаждать быстро. Однако в случае кристаллизации больших масс сплава практически это сделать трудно. Тогда в целях предотвращения возникновения ликвации по удельному весу в сплав вводят третий компонент с таким расчетом, чтобы эта добавка образовывала с одним из основных компонентов химическое соединение. Будучи более тугоплавким, оно начнет при охлаждении сплава выделяться в первую очередь и своими тонкими, сильно разветвленными осями дендритов воспрепятствует разделению структурных элементов сплава по высоте отливки.
Иногда наблюдается явление расслоения одной жидкой фазы на две различные по составу жидкости с последующим возникновением различной структуры по высоте отливки, которое является разновидностью ликвации по удельному весу. Расслоение наблюдается в сплавах с ограниченной растворимостью компонентов в жидком состоянии (например, сплав системы свинец – цинк).
Быстрое охлаждение сплава от температуры расслоения мало влияет на уменьшение этой ликвации. Высокий нагрев сплава до однофазного жидкого состояния и последующее быстрое охлаждение, тщательное перемешивание и встряхивание являются приемами, препятствующими явлению расслоения и возникновению зональной ликвации по высоте отливки.5.2. Коррозионная стойкость
Это способность металла сопротивляться разрушению под химическим воздействием окружающей среды.
Чисто химическая коррозия определяется главным образом окислением, электрохимическая коррозия возникает из-за физико-химической неоднородности металлов в присутствии жидкости, способной проводить электрический ток.
Электрохимическая активность металлов характеризуется электродным потенциалом, измеренным относительно водорода (табл. 5.2)
Таблица 5.2
Электрохимический ряд напряжений
Каждые два металла образуют гальваническую пару. При этом электродвижущая сила будет тем больше, чем дальше друг от друга они стоят в электрохимическом ряду.
Для предупреждения коррозии используют различные методы защиты. Очень большое значение имеет борьба с коррозией в деле охраны и реставрации высокохудожественных памятников искусства – статуй, барельефов, металлического декора архитектуры, оград, ворот и т. п.
Для защиты от коррозии художественных изделий из металла применяют следующее: 1) рациональное конструирование; 2) устранение возможности коррозии при производстве, транспортировке и хранении; 3) технологические методы.
Рациональное конструирование. При проектировании художественных изделий из металла целесообразно таким образом разрабатывать конструкцию, чтобы возможность электрохимической коррозии исключалась. Для осуществления этой задачи необходимо:
подбирать металлы с близкими потенциалами;
применять соответствующие прокладки между деталями из металлов с различными электродными потенциалами, исключающие возможность контакта;
конструировать такие формы, в которых не может задерживаться влага (электролит).
Устранение возможности коррозии при производстве, транспортировке и хранении. Появление коррозии на изделиях художественной промышленности часто обусловлено несовершенством или нарушением технологических процессов. Например, в литейных цехах причиной появления коррозии могут служить загрязненность формовочных смесей, плохая очистка от формовочной земли, несвоевременность сушки при водяной очистке и т. п. В механических цехах коррозия может возникнуть при неправильном подборе охлаждающих эмульсий или смазок.
Очень важно тщательно очищать изделия от остатков флюса после пайки или сварки, так как флюсы в большинстве случаев имеют кислую реакцию и разъедают металлы. По своей природе сварной или паяный шов представляет собой гальванопару с металлом изделия, и при наличии следов флюса, играющего здесь роль электролита, возникновение электрохимической коррозии неизбежно.
Лучше всего противостоят коррозии полированные изделия, поэтому в отделочных цехах необходимо следить, чтобы на гладких поверхностях художественных деталей не оставалось царапин, трещин и других дефектов.
При транспортировке и хранении готовых художественных изделий из металла следует принимать профилактические меры, направленные против возможности возникновения коррозии. Для стальных изделий, а также изделий, изготовленных из алюминиевых и магниевых сплавов, применяют защитные смазки, имеющие нейтральную реакцию (не содержащие свободной кислоты). Все виды изделий хранят в сухих помещениях или применяют водонепроницаемую тару, так как от воды корродируют не только черные, но и цветные металлы.
Технологические методы защиты от коррозии. При производстве художественных изделий из металла технологические методы защиты от коррозии неразрывно связаны с декоративной отделкой изделий. Как правило, в художественной промышленности применяются только такие технологические методы борьбы с коррозией, которые одновременно являются и декоративной отделкой. Поэтому благодаря применению того или иного приема защиты от коррозии художественные изделия не только не теряют своего внешнего вида, а, напротив, приобретают новые художественные качества – цвет, блеск и т. п.
Основными технологическими методами защиты художественных изделий от коррозии являются:
а) легирование – введение в корродирующие металлы и сплавы при их производстве дополнительных элементов, сообщающих всему сплаву стойкость против коррозии, например – хромоникелевые стали (нержавеющие стали);
б) оксидирование – искусственное образование химическим путем на поверхности изделий стойких пленок, защищающих их от коррозии;
в) металлические покрытия – способ, когда сплавы и металлы, менее стойкие против коррозии, закрывают более стойкими и, кроме того, обычно более декоративными, например хромирование, никелирование, золочение и др.;
г) неметаллические покрытия изолируют металлические изделия от внешней среды и тем самым препятствуют возникновению и развитию коррозии5.3. Ковкость
Ковкость – свойство металла изменять свою форму под действием ударов или давления, не разрушаясь. Степень ковкости зависит от многих параметров. Наиболее существенными из них являются следующие: пластичность, степень нагрева, величина деформирующего усилия, наличие примесей и др.
Металлы могут коваться как в холодном состоянии, например красная медь, золото, так и в горячем, например сталь. Это свойство широко используется при изготовлении художественных кованых изделий из малоуглеродистой стали (ранее называемой ковочным железом). Малоуглеродистая сталь, раскаленная докрасна, становится настолько пластичной и мягкой, что из нее можно изготовлять художественные изделия самой разнообразной сложной формы.
5.4. Свариваемость
Свариваемость – способность металла прочно соединяться путем местного нагрева и расплавления свариваемых кромок изделия. Чистые металлы свариваются легче, а сплавы труднее. Легко свариваются изделия из малоуглеродистой стали. Чем выше процент содержания углерода в стали, тем хуже ее свариваемость. Наиболее затруднительной считается сварка высокоуглеродистых легированных сталей, и особенно чугуна.
5.5. Спекаемость
Спекаемость – свойство, в результате которого образуется металлокерамика. При этом металлы, предварительно измельченные в порошок, смешиваются, запрессовываются в специальные формы и подвергаются действию высокой температуры и давления до спекания. Различные металлы спекаются неодинаково – одни лучше, другие хуже. Способом спекания сейчас производят особо твердые стойкие сплавы, например победит, который применяется при изготовлении режущих инструментов.
5.6. Обрабатываемость резанием
Обрабатываемость резанием на различных станках (токарном, фрезерном и пр.), а также способность шлифоваться и полироваться – это свойства, играющие существенную роль в производстве художественных изделий и особенно в отделке (полировании). Хорошо режутся бронзы, латуни и некоторые марки сталей, алюминия и чугуна. Плохо обрабатываются на станках детали из красной меди и из свинца и его сплавов.
Черный Маг Императора 9
9. Черный маг императора
Фантастика:
юмористическое фэнтези
попаданцы
аниме
рейтинг книги
Не грози Дубровскому! Том II
2. РОС: Не грози Дубровскому!
Фантастика:
фэнтези
попаданцы
аниме
рейтинг книги
Идеальный мир для Социопата 7
7. Социопат
Фантастика:
боевая фантастика
рейтинг книги
Бремя империи
Бремя империи - 1.
Фантастика:
альтернативная история
рейтинг книги
Приручитель женщин-монстров. Том 5
5. Покемоны? Какие покемоны?
Фантастика:
юмористическое фэнтези
аниме
рейтинг книги
Мастер...
1. Мастер
Фантастика:
героическая фантастика
попаданцы
аниме
рейтинг книги
Эфемер
7. Стеллар
Фантастика:
боевая фантастика
рпг
рейтинг книги
Приручитель женщин-монстров. Том 4
4. Покемоны? Какие покемоны?
Фантастика:
юмористическое фэнтези
аниме
рейтинг книги
Идеальный мир для Лекаря 3
3. Лекарь
Фантастика:
фэнтези
юмористическое фэнтези
аниме
рейтинг книги
Дракон
5. Совсем не герой
Фантастика:
фэнтези
попаданцы
рейтинг книги
Не грози Дубровскому! Том V
5. РОС: Не грози Дубровскому!
Фантастика:
фэнтези
попаданцы
аниме
рейтинг книги
Первый пользователь. Книга 2
2. Первый пользователь
Фантастика:
боевая фантастика
рпг
рейтинг книги
Последний попаданец 9
9. Последний попаданец
Фантастика:
юмористическая фантастика
рпг
рейтинг книги
Запретный Мир
1. Запретный Мир
Фантастика:
фэнтези
героическая фантастика
рейтинг книги
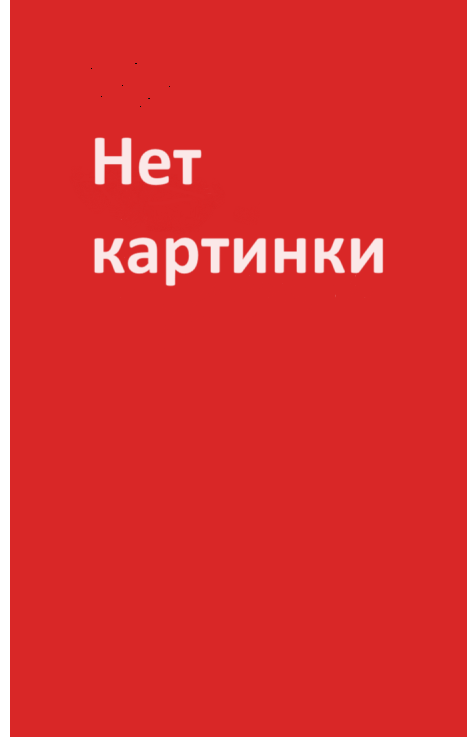