Современная дамасская сталь
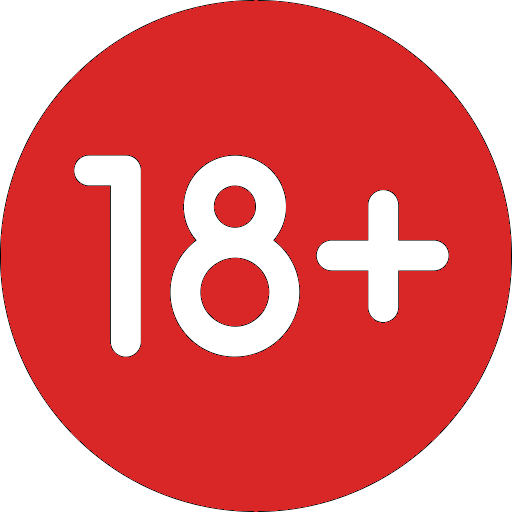
Шрифт:
Ни один материал в истории, может только за исключением булата, не был окутан таким флером романтики и мифов, как дамасская сталь. Оружие из него ковали полулегендарные народы, им повергались тираны, драконы и мифические чудовища. Клинки из него рубили доспехи, вековые дубы и даже камни. Что тут правда, а что преувеличение? Попытаемся найти ответ на этот вопрос.
Немного истории
Дамасская сталь появилась в начале железного века. Стоит указать, что никакой исключительности в распространении дамасской стали не отмечено. Было замечено, что путем сварки и складывания науглероженных слоев железа можно получить сталь, которая воспринимает закалку и служит сырьем для изготовления великолепных инструментов и оружия.
Почти все мировые культуры использовали дамасскую сталь. Технологией ее изготовления владели кельтские и саксонские племена. Мечи викингов демонстрируют сложную структуру узора. Одна из высших форм такой стали производилась в Японии. Японцы в ходе процесса именуемого tamahagane производили мечи исключительной красоты и качества. Дамасские клинки из Средней Азии общеизвестны, они производились и на Балканах, и на Кавказе. Их делали во Франции, России и Турции. В Германии во время Второй Мировой войны большое количество клинков из Дамаска было произведено для нужд военных. Этой технологией владели и продолжают владеть мастера Малазийского архипелага "эмпу": крисы с особым слоистым рисунком клинка до сих пор производятся по древним технологиям. В Средней Азии изготовление ножей из Дамаска не прерывалось даже в годы Советской Власти. Но, тем не менее, возвращение моды на нее произошло только в 70-х годах. Bill Могап представил первый нож из Дамаска миру коллекционеров на шоу Ассоциации Ножовщиков (Knifemakers Guild show) в 1973 г. Другие тоже работали с этим "новым" материалом - Robbin Hudson, Jim Wallace и Robert Griffith. В это же время Daryl Meier, возглавлявший исследовательскую команду "Damascus research team", начал длительное изучение загадок
Наметившийся в конце XX века ренессанс в изготовлении Дамаска вызвал к жизни и огромное количество спекуляций на этой ниве. Как ни странно это звучит, по настоящему качественный рабочий Дамаск, в отличие от декоративного, производят единицы. Главной причиной этого видится малая информированность и коммерческая раскрученность данного направления: спрос рождает предложение, и на рынке появляется все больше и больше изделий из материала, отнести который к дамаску можно только по внешнему виду. Недостаток информации обусловил ряд заблуждений, господствующих в массовом сознании. В качестве главной характеристики дамасской стали, определяющей ее достоинства, обычно называют чередование слоев с высоким содержанием углерода, придающим клинку остроту, и низким, придающим ему прочность. На самом деле, в ходе кузнечной сварки слоев стали с разным содержанием углерода, имеет место его диффузия (т.е. перемещение из областей с высоким содержанием в область с низким). Это ухудшает режущие свойства высокоуглеродистых составляющих пакета за счет обеднения по углероду, а по некоторым данным (С.А. Федосов "Механические свойства сварочной дамасской стали современной выделки"; Ргос. of Int.Conf. "Techno-logy 99", STU Bratislava, 8-9 Sept.1999, v.l, pp.50-52) из-за обилия сварочных швов даже могут снижаться и прочностные свойства клинка. Кроме того, выгорание углерода при многократной кузнечной сварке может уменьшать его содержание на 0.3 -0.4%. Дабы компенсировать такие значительные потери, многие мастера идут на более жесткие режимы закалки. Другой способ - брать для пакетов только такие составляющие, каждая из которых сама по себе способна обеспечить хорошие режущие и прочностные свойства клинку. Энтузиасты дамасской стали указывают на то что в итоге кузнечной сварки образуется качественно иная структуру металла, состоящая из переплетенных железных и стальных слоев или волокон. Выбор оптимального соотношение железа и стали или сталей разных марок, температурного режима, а также характер сочетания слоев в полученном композите могут обеспечить такое сочетание прочности клинка и стойкости режущей кромки, которое практически недостижимо на обычных сталях. Однако, одновременно, они признают и тот факт, что создание такого композита требует от изготовителя величайшего мастерства и многолетнего опыта. Популярное заблуждение гласит, что для пакета древние мастера брали очень дорогие и секретные марки стали, которые и образовывали редкие по красоте узоры. Но известны клинки уже XIX века из Германии и Франции, на которых легко читаются даже внедренные в узор буквы и цифры. Современным мастерам, владеющих технологией кузнечной сварки, создать подобные узоры тоже не представляет особых затруднений. Красота дамасских сталей в своей основе имеет различие цветов слоев с разным составом. Для ярких линий у стали должен быть высокий уровень хрома или никеля. Для темных линий могут применяться простые углеродистые или даже низкоуглеродистые стали. Если они особенно тонкие, то можно добавить серые тона путем варьирования состава высокоуглеродистых сталей в пакете. Самой распространенной и простой является сварка сложенных стопкой пластин, образующих пакет. Пакет нагревают в горне и посыпают тем или иным флюсом, который сплавляется с образовавшейся на поверхности пластин окалиной и очищает от нее свариваемые поверхности. Растворяя окалину, флюс одновременно образует жидкий шлак, предохраняющий поверхность металла от дальнейшего окисления. Покрытый жидким шлаком пакет разогревают до белого каления и проковывают. Сначала выжимают жидкий шлак, а затем сильными ударами производят собственно сварку. После первой сварки пакета его расковывают на полосу и разрубают на несколько частей, которые снова складывают стопкой и производят вторую сварку. Эти действия повторяют до тех пор, пока не наберут желаемое количество слоев железа и стали в изделии. Больше всего ошибок с именно определением количества операций при создании пакета: количество сварок соотносится к количеству слоев не прямо пропорционально, а в геометрической прогрессии. Например, начав со сваренной из 4 слоев заготовки, первое сворачивание и сварка даст 8 слоев, вторая -16, третья - 32, 4 - 64, пятая - 128, шестая - 256, а седьмая - 512. С другой стороны, есть объективные физические законы, которые не дают создавать пакеты с количеством слоев более 40- 50 тысяч. Howard Clark произвел ряд экспериментов и выяснил, что при многократном сворачивании углерод имеет тенденцию к выравниванию своей концентрации по всему объему пакета вследствие диффузии, в конечном итоге формируя квазигомогенную заготовку. Господствует мнение, что качество дамасской стали прямо пропорционально количеству слоев (и, соответственно, числу сворачиваний и сварок). Это справедливо для популярного в XIX веке и ранее процесса рафинирования стали, который имел целью получение однородной структуры, но при изготовлении Дамаска из современных, достаточно качественных исходных материалов, это подчас просто потеря времени и сил. Да и с увеличением количества слоев возрастает риск появления брака. Иногда для изготовления качественного прочного пакета достаточно всего нескольких операций по складыванию и сварке. Таким образом, даже диффузия углерода становится на службу мастеру, помогая избежать наличия крупных низкоуглеродистых областей на режущих кромках. Оптимальным для дальнейшего развития узора считаются пакеты с 300 ~ 500 слоями. Взяв пакет с количеством слоев, близким к 1000 вы рискуете получить чересчур тонкий узор; а взяв пакет с количеством слоев менее 300 наоборот - слишком толстый и широкий. Конечно, из этого правила есть и исключения, но в конечном итоге все зависит от квалификации кузнеца. Когда пакет сформирован, можно создать несколько основных типов узоров.
Традиционный дамаск
Наиболее полная и развернутая характеристика типов традиционного Дамаска дана Л. Б. Архангельским в статье "О булатах и булатных клинках" (журнал Металлург #8,1999). "В коллекционных образцах оружия нередок так называемый "дикий" узор да-маска, образующийся в результате случайного перемешивания металла в результате ручной ковки... Однако многие мастера предпочитают ковать клинки из "штемпельного" Дамаска с его регулярным узором. "Штемпельным" узор назвали в Германии по способу его образования путем набивки специальным штампом-штемпелем строго упорядоченного рельефа на заготовку клинка, после сошлифовки которого слои искажаются в заданном порядке. Видов этих узоров немного и большинство из них были известны еще в прошлом веке. К ним относятся ступенчатый, волнистый, ромбический (сетчатый) и кольчатый.
Ступенчатый узор характеризуется относительно узкими прядями линий, расположенными поперек клинка. В зависимости от размеров рельефа, тщательности отковки и шлифовки клинка узор может представлять собой либо концентрические овалы, либо разомкнутые, волнистые фигуры, напоминающие ряд сосулек или сталактитов, свисающих с обуха клинка. Распространенным видом "штемпельного" узора является ромбический, имеющий две разновидности. Одну из них получают, насекая поверхность заготовки зубилом крест-на-крест, отчего узор имеет вид сплетенной из нитей сетки, наброшенной на клинок из "дикого" Дамаска. Соответственно, и узор называется "сетчатым". Второй разновидностью является узор, который в Германии называют "мелкие розы". Он имеет вид четких концентрических ромбов и набивается имеющим пирамидальные выступы штампом, похожим на кулинарный молоток для отбивания мяса. Третий, кольчатый вид "штемпельного" узора в США называют "павлиний глаз", поскольку на клинке в четком порядке расположены многочисленные концентрические окружности. Некоторые современные мастера по разметке засверливают непосредственно саму заготовку клинка, другие делают то же самое со штампом, которым и набивают этот узор, когда потребуется. Похожий до неразличимости узор получается, если на заготовке клинка нарезать, а не насечь, сетчатообраз-ный рельеф с высокими квадратными выступами. При расковке эти квадраты вдавливаются и расплываются, образуя регулярный кольчатый узор. Многие мастера в совершенстве овладели и методами изготовления различных разновидностей столь красивого металла, как "турецкий" дамаск. Отличительной особенностью разновидностей "турецкого" или "харалужного" Дамаска являлось то, что клинки отковывались из предварительно туго закрученных прутков неоднородного металла. Узоры при этом получались крайне разнообразными и причудливыми, но технологические приемы их получения можно систематизировать и сгруппировать по мере усложнения изготовление клинка: из одного слоистого закрученного прутка; из одного ряда прутков, закрученных в разные стороны; из таких же прутков, но расположенных в два ряда таким образом, что разные его части откованы с использованием крученого Дамаска разного вида.
Мозаика
Особую популярность приобрел в последние годы мозаичный дамаск. Steve Schwarzer, Pierre Reverde, Daryl Meier
Развитием этого направления является метод предложенный Steve Schwarzer и позволяющий получать качественный провар пакета. Он заключается в том, что сварочный контейнер имеет полую трубчатую рукоять на холодном ее конце. Контейнер вакуумируется и заполняется азотом или инертным газом.
Процедура заполнения производится несколько раз перед сваркой для полного удаления кислорода из внутренних полостей. Используя такой метод возможно сварить даже те металлы, который не поддаются сварке на открытом огне.
Steve Schwarzer и Pierre Reverde являются разработчиками особой методики, которая требует современных инструментов для создания сложных мозаичных узоров. С помощью электродугового резака рисунок прорезается сквозь стальной блок, после чего из другого блока вырезается фасонный вкладыш для заполнения вырезанной полости. Далее они свариваются диффузионной сваркой в единый элемент. Некоторые удивительные детали, невозможные ранее, могут быть получены в такой технике "глубокой инкрустации".
Barry Gallagher, Shane Taylor и Rick Dunkerly путем комбинирования разных техник создали совершенно новую категорию мозаичного дамаска с использованием сложения пакета и его сварки с применением фасонных штампов. Прообразом послужил оригинальный узор созданный Darrel Meier под названием "Коленкор". Совместными усилиями они создали новую технику узора по стали. Современный промышленный дамаск Промышленное производство дамасских сталей, в основном, базируется на тех же принципах, что и авторского Дамаска. Некоторые считают его безличным и однообразным, но высокий спрос на полуфабрикаты при низком уровне предложений со стороны индивидуалов стимулировал развитие этой отрасли промышленности. Современный рынок промышленного Дамаска крайне неоднороден - от малосерийных образцов из мастерских известных мастеров (как, например, используемых на малосерийных проектах компании Cold Steel) до массового производства промышленных предприятий, берущих на работу популярных изготовителей авторского Дамаска. Тем не менее мощное технологическое оборудование {промышленные кузнечные прессы, вакуумные прокатные станы, электродуговые печи с контролируемой атмосферой, газо-статы и т.п.) позволяют создавать не только достаточно качественные сварные пакеты для трехслойных клинков как у Helle и Frosts а также San-Mai у Cold Steel, но и неплохой серийный дамаск. Применение вакуумных технологий помогло решить проблему ограниченности исходных материалов для производства дамасской стали. Поскольку окисления предварительно зачищенных поверхностей при нагреве в вакууме не происходит, то становится возможной сварка высоколегированных, в том числе нержавеющих, сталей без флюса. Соединяемые отшлифованные пластины свариваются методом диффузионной сварки в вакуумной камере под прессом. Сваренный таким образом пакет расковывается на пластины, которые снова шлифуются, свариваются и так до тех пор, пока не получится нужное количество слоев. Этим методом можно изготавливать дамаск из нержавеющих, быстрорежущих и иных легированных сталей. Высокопроизводительным методом сварки высоколегированных сталей является прокатка пакета шлифованных или очищенных другим методом пластин на вакуумном прокатном стане. Для сварки металлических волокон и гранул применяют технологии, используемые в порошковой металлургии. В наполненную инертным газом камеру газостата помещают вакуумированную и герметическую капсулу, наполненную проволокой, металлическим порошком или смесью того и другого. Затем нагревают капсулу до 1200-1400°С и заполняют камеру газом до тех пор, пока давление в ней не достигнет примерно 1500 атм. После завершения процесса спекания композитного материала под давлением, спекшуюся с композитом оболочку удаляют механическим путем и очищенный композит проковывают или прокатывают. Этим высокопроизводительным методом можно получить практически любую из известных структур Дамаска. Одним из наиболее известных крупных производителей дамасской стали несомненно является шведская компания DAMASTEEL АВ, образованная в августе 1995. Ее специализация - изготовление современными методами заготовок из дамасской стали для нужд серийных производителей и индивидуалов. Время зарождения этого производителя - ноябрь 1992 г., когда сотрудничество между производителем порошковых сталей Soderfors Powder АВ и индивидуалом-кузнецом Каем Эмбертсеном из шведского города Эдсбина оформилось в отдельный проект. Успешный метод по созданию дамасской стали на основе достижений порошковой металлургии был разработан в течение 1993 г., а в 1996 был получен патент на изготовление заготовок из порошкового Дамаска. DAMASTEEL АВ производит методом порошковой металлургии два типа полуфабрикатов - прутки со слоистым концентрическим рисунком, напоминающим в разрезе годичные кольца деревьев, и многослойный пакет с параллельными слоями. В дальнейшем полуфабрикаты могут использоваться для создания более сложных узоров в процессе ковки. При этом развитие узора из заготовок с "древесной" структурой происходит за счет фрезерования или штамповки, а плоскослоистой - как для фрезерования и штамповки, так и для кручения. В ходе ковки узор может быть усложнен и улучшен. Дальнейшее развитие узора может производиться уже самим покупателем на основе собственных промышленных мощностей, хотя на конечную закалку рабочий дамаск предпочитают возвращать производителю. Промышленный Дамаск охотно приобретают не только крупные серийные производители, такие как Bear MGC, Heinr. Boeker Baumwerk GmbH и Niet-одля использования на эксклюзивных моделях, но и такие мастера как Michael Walker, Barry Gallagher и многие другие. Приведенные примеры далеко не полностью исчерпывают достижения исследователей узорчатых металлов в применении новейших технологий. Эти технологии дают возможность использовать при изготовлении Дамаска любые высокопрочные легированные стали, что резко повышает функциональные свойства изготовленного из него клинка.
Заключение
Так что можно порекомендовать человеку, который хочет приобрести клинок из Дамаска? Во-первых, риск брака на Дамаске намного выше, чем на клинке из обыкновенной стали. Это происходит по причине сложности и длительности процесса его изготовления. Недокал и перекал, непровар и обезуглероживание, ошибки при сборке исходного пакета -вот далеко не полный перечень проблем, которые могут полностью перечеркнуть результат длительных трудов. Да и что греха таить - подчас даже опытные мастера дают себе поблажку и собирают пакет с упором на его внешнюю красоту, но не на рабочие свойства. В результате клиенты мучаются с клинком со средним значением углерода не выше 0.3 -0.4% или даже вообще с незакаленным пакетом. Есть марки сталей, столь сложные в обработке, что малоопытные мастера их избегают. Теперь представьте, что в вашем пакете несколько таких сталей. Каждая имеет свои собственные температуры сварки и закалки. Комбинации из трех и более сталей налагают еще более жесткие требования на их термообработку - подчас при неверно выбранном режиме, под действием внутренних напряжений, вызванных неоднородностью структуры, клинок деформируется или лопается, иногда сразу, а иногда - при первом же легком ударе. Иногда наоборот - режущая кромка сминается при первом же контакте с чем-то более твердым, чем масло. Таким образом, попытка связать несколько металлов в едином пакете сродни задаче "запрячь в телегу коня итрепетную лань". Перед приобретением авторского дамаска попытайтесь понять точку зрения самого мастера на свой продукт. Два крайних случая: мастер, который дрожит над каждым кусочком своего материала, как скупой рыцарь, и мастер, который безжалостно отправляет "не показавшийся" ему кусок в большое ведро, уже набитое битком неудачными продуктами поиска. Всегда выбирайте второго - первый просто не производит Дамаска в достаточном количестве, вот и дрожит над каждым, даже в высшей степени проблемным, куском, в то время как второй предъявляет к своей работе самые жесткие стандарты, постоянно совершенствуя и развивая свою технику. Спросите мастера, из чего он кует клинки. Если прозвучит фраза о старых напильниках, стальных тросах, цепях, рессорах и пружинах, то изделий этого мастера стоит избегать. Изготовление современного Дамаска базируется на определенных марках сталей с определенным процентным составом, и помимо индивидуального мастерства, опыта и интуиции отталкивается еще и от теоретического металловедения. Особо стоит избегать тех, кто переводит разговор о своем материале на историко-мифологические темы или начинает беспардонно нахваливать самого себя. Правда о Дамаске заключается в том, что у знающего и опытного мастера он может получиться совсем не хуже по свойствам, чем клинок из любой составляющей пакета, но ожидать каких то магических сверхсвойств не стоит. Более того, - если мастер не слишком опытен, попытка сварить стали с высокой прочностью и хорошей стойкостью режущей кромки, может закончиться непрочным клинком с недолговечным лезвием. Главная ценность Дамаска в его удивительной, гипнотической красоте застывшего в металле пламени. В удивительных изгибах и завитках угадывается летний лес и зимняя пустыня, водная гладь и штормовые валы. Именно это вдохновляло создателей мифов и легенд и звало воина на битву. Именно это придает дамасскому клинку непередаваемую, вневременную красоту, в которой осталась частичка души сделавшего его мастера. Именно в этом его магия.